40K HOBBY: One Meks Step-by-Step Guide to Lootin’ – Part 1
8 Minute Read
Dec 9 2011
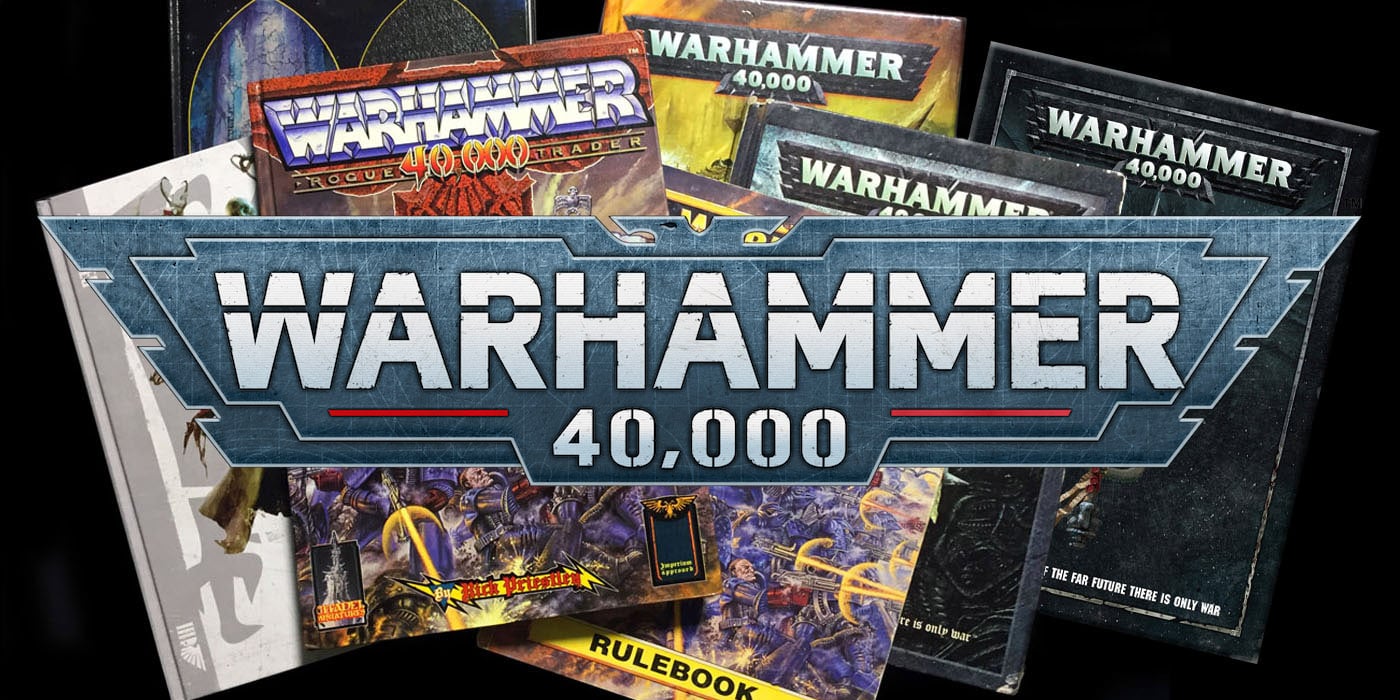
Advertisement
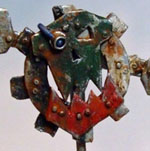
I admit my plans changed for this article as initially I was going to convert something for my own Ork force but it turned out all the options either lacked enough scope or were far too involved.
Inspiration hit however during a sort out when I decided I have too many tanks sitting unfinished and it would be best to clear some out. Killing two birds with one stone I set out to loot these three Leman Russes before clearing them out.
Materials & Tools.
Our starting point is not with the models but with the materials and tools I use.
The most important material used in converting is sheet styrene, commonly known as plasticard. It is also available in textured sheet, strip, rod, tubes and various other forms. For the bulk of any conversion I use 1mm sheet. Strong, yet easy to work with. 0.5, 0.75 & 0.25mm I generally use for detailing. While sheet can be cut into strips I find having styrene strip on hand very useful as it gives you a material which is accurate and consistent dimensionally. Rods and tubes are pretty self explanatory. Good for piping, barrels, exhausts, hinges, rivets and a host of other things.
![]() |
Any offcuts I get are chucked into these trays – 1mm, 0.5mm, 0.25mm, textured sheet, strip/rod |
You should never throw an offcut away. They are perfect for small detail work or for internal support pieces – small offcuts glued behind panels or at joints to give extra strength or to help pieces line up. You will see a lot of these in the pictures to follow.
Mesh for viewports, stowage baskets and dodgy Orky repairs. Brass rod is great for pinning pieces and is a better option than styrene rod for banner poles, grab handles etc. Neodymium (Rare Earth) magnets ideal for when you want to keep pieces removable such as weapons and krew. Pins and scale model chain are for exactly what you think.
The majority of the tools I use are shown below:
A – Steel rulers & engineers squares.
B – Knives with spare blades.
C – Pliers & cutters.
D – Pin vice with drill bits.
E – Wet & Dry sandpaper & needle files.
F – Green Stuff & sculpting tools.
G – Circle cutter.
Advertisement
H – Tweezers
I – Polystyrene cements, superglues & two part epoxy.
J – Hobby G-clamps.
K – Razor saws & cutting blocks.
L – Scissors
M – Hole punches.
N – Vernier.
O – The Chopper II
P – ‘True Sander’
The most essential items are the knives, steel rulers, engineering squares and the glues, these are probably involved in 90% of the work in any conversion I do. Many of the items are standard modelling gear; while others I won’t use often but can be big time savers. The few items on there you might not have expected are:
Circle cutter – designed really to cut paper and thin card but it can be used to cut thin styrene and to score a line on thicker sheets.
Hole punches, the smaller two are paper punches while the larger is a leather punch.
Vernier for accurate measurements of models and materials.
Chopper II & ‘True Sander’. Two very handy items. The former allows you to cut accurately and consistently, but on an Ork build I don’t use it that much. True Sander is very useful for squaring off pieces.
A Few Basic Techniques.
I thought it best to show a couple of general techniques which will be used throughout the conversions, namely Cutting Styrene, OrkyRivets, Glyphs and Handles.
Cutting Styrene:
To cut styrene I always use a straight edge to act as a datum from which all other dimensions will be taken. If the piece of styrene has no straight edge you can use the ‘score-and-snap’ technique below to cut a thin piece off the sheet to give a straight edge you can use.
Use a steel ruler to measure from the straight edge; I will often butt an engineers square against the edge for ease. Make a small dimple in the styrene with a knife tip. Repeat this at least one more time further up the styrene.
Line up a steel ruler by putting the knife tip into the dimples in turn and butting the ruler up against the blade. Do not cut through but instead score the styrene by running the knife firmly down the ruler 2-4 times.
The styrene can now be bent and it will naturally hinge along the scored line. If it doesn’t come apart straight away just bend the styrene back as it will do.
As you can see the styrene is approx 0.5mm oversized – I expect this to be the case. It is better to have the styrene be a fraction over than under as you can gently sand the piece back until you get a perfect fit. With Ork builds it doesn’t particularly matter if I am honest as anything can be incorporated into the ramshackle nature of Ork engineering.
Along a cut edge you will get a ‘ridge’, this can be cleaned up either with some wet and dry sandpaper or by running a knife blade along it much like a mould line.
Orky Rivets.
Rivets are easy and straight forward though they can be time consuming.
I tend to use 1mm and 1.6mm rod for Ork tanks as I like the mix. Using these sizes allows the Ork rivets to stand out from the smaller, rounded Imperial rivets. On occasion I will also use 0.88 or 1.2 rod, especially when mixing GW Ork parts on a conversion. I cut each rivet from styrene rod aiming for 0.5mm thickness, but not really worrying much. Any too thin or thick are discarded.
To apply poly cement is brushed on and the rivets are picked up and gently put in place with the tip of a knife. You can add several before the glue dries up or use the time to move a rivet into position. I will brush more poly cement over the rivets to firmly set them in place.
If there is a rivet I’m not happy with it gets cut off and replaced.
![]() |
Comparing Ork and Imperial rivets. |
Glyphs and Dags
Glyphs are very easy to do and are a great way to add some Orky charm to a build. The glyph design is drawn roughly onto a piece of offcut styrene before cutting it out with a knife. The shape is then refined, trimming as required and cleaning up the edges. Once the glyph is distressed it is glued either in position on a vehicle or to a mounting plate which can then be positioned on a vehicle, to finish off some rivets are added. Dags are simply triangles of styrene which I often cut from a long offcut as shown. Each triangle is distressed and then glued in place with a rivet.
Handles / Grab Handles
I prefer to do handles in 1mm brass rod as styrene is too prone to breaking during painting or gaming.
Using long nosed pliers I bend the rod into shape before snipping it free. Using the handle as a guide holes can then be drilled into the model. With superglue on each end pliers are used to carefully push the handle into the holes, it’ll be a tight fit but care needs to be taken not to push the ends in too far.
When deciding on the height (‘h’) it is best to err on the side of caution – if they are longer than needed it can be pushed further into the holes, but too short and you’ll need a new handle.
The Lootin’ Begins
The first task was stripping back the models to give me a base to build upon. Anything I removed went into the bitz box; some pieces are destined to be re-used on these vehicles while the rest will stay in the bitz boxes for future use.
I generally don’t do mock ups except for commissions or large builds, however for the article I decided to do some as it will hopefully show how they can be beneficial, especially when you first start looting vehicles, and having them will also show how my initial designs develop from the first step up to the finished builds.
![]() |
Mock ups held together with blu-tac and tape |
While each Looted Wagon will have an ‘Ard Case and a Boomgun the aim is to have three individualistic looking models.
A – Built up hull with a looted Russ turret.
B – Rebuilt hull incorporating weapons.
C – Plating to the hull, new exhausts & scratch built turret.
One wagon will have a Reinforced Ram while another will have engine detail.
A mock up can help you refine your ideas, for example it is better to decide now a rough size of a turret than waste styrene making the first version too large. While you always want a build to develop organically as it progresses having a solid starting point will help cut out much of the pontificating and indecision you may later experience when building the tank for real.
That is the end of Part One. In Part Two I crack on with the first Looted Wagon – The Destroyer Tank Hunter inspired design. If you have any questions about what Part One please post them up or drop into Recalcitrant Daze for a number of completed Looted vehicles.
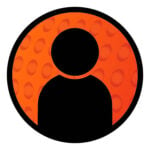
Author: Rictus
Advertisement